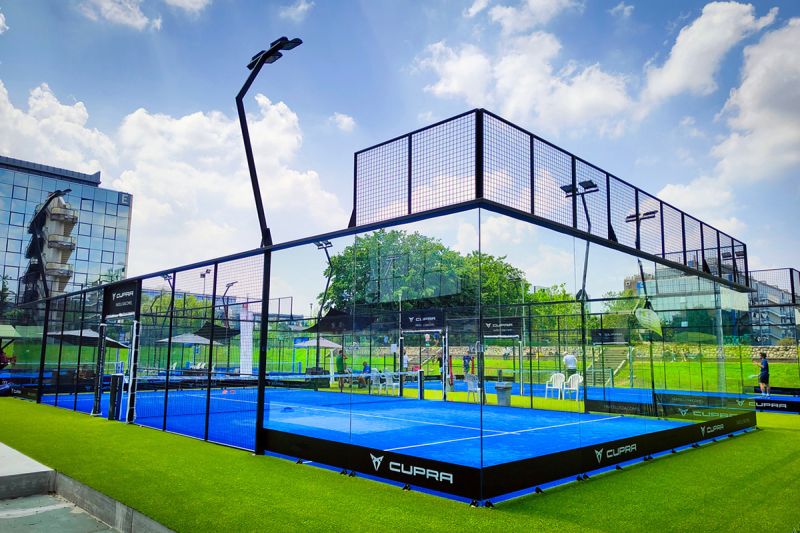
The (Italgreen) Court
Siamo andati a visitare dove nascono i campi Italgreen, tra le aziende leader del settore. Un processo complesso che richiede professionalità e un forte grado di automazione. Perché solo in apparenza i campi sembrano tutti uguali…
Lo scrittore (e architetto) svizzero Max Rudolf Frisch l’ha spiegato con estrema chiarezza: «Un robot riconosce la realtà meglio dell’uomo, calcola il futuro, non fa speculazioni e viene guidato dai propri risultati. E soprattutto, non può sbagliarsi». Da quando nel 1738 è stato creato il primo esemplare (da Jacques de Vaucanson, suonava il flauto perfettamente), la robotica ha fatto strike nella nostra vita, determinando gran parte delle nostre azioni. Il padel non fa eccezione: si prenota il campo con una app, si organizza una lezione con whatsapp, si crea una league con una chat, tanto per fare esempi pratici. Ecco, lo stesso paradigma vale quando si deve produrre un campo, con particolare attenzione alla struttura in acciaio, quella che permette di giocare in sicurezza, se il lavoro è svolto come Dio comanda. Una sollecitazione a cui ha risposto Italgreen, una delle aziende leader nel panorama italiano (ma non solo, stay tuned) che ci ha mostrato la sua filiera produttiva. La scelta di carpenteria, zincatura e verniciatura, è ricaduta su aziende del suo territorio (provincia di Bergamo) e assicurano qualità, precisione e affidabilità. Per riuscirci, si è accantonata qualsiasi forma di robofobia, come ci ha riassunto il CEO, Daniele Gilardi, con un assunto difficile da contestare: «Più la produzione è meccanizzata, migliore è la qualità del lavoro e minore è il margine di errore».
Il nostro viaggio è cominciato in carpenteria, la vera anima nella costruzione di un campo, dove si respirano ferro e lavoro. Però con supporti un tempo impensabili (e ancora adesso abbastanza rari): «Per tagliare i profili in acciaio del campo, utilizziamo un impianto meccanizzato per una semplice ragione: la precisione e l’affidabilità nel tempo perché la macchina non si stanca mai, dovesse lavorare h24 – ci racconta Nicola Pedruzzi, responsabile tecnico di Italgreen -. A monte c’è una progettazione in 3D che viene passata a una macchina intelligente che lavora su tre assi, con un laser che realizza le varie sagomature e forature. Per lo spessore dei profili, stiamo passando ai quattro millimetri perché consente una sezione più stretta e lineare, esteticamente più accattivante, sempre nel pieno rispetto della NTC 2018». Una scelta comprensibile perché siamo pur sempre italiani e strizziamo l’occhio al design. Per gli appassionati di carpenteria, il processo comincia caricando automaticamente le barre che la macchina cattura una per volta; si prosegue con la penditura, una sorta di impiccagione dell’acciaio, con un sensore che svolge una pre-misura in modo che il materiale faccia ritorno con le giuste tolleranze. Una volta ricevuto il consenso, la barra viene movimentata e pinzata da un mandrino. Man mano che il laser lavora, il mandrino porta avanti la verga e viene lavorato il pezzo.
La certezza che ogni barra abbia lo stesso profilo e misure è dato dal taglio laser che ha una tolleranza di tre decimi di millimetro. Il processo appare complesso ma l’automazione aiuta, tanto che basta impiegare tre persone: «Una che si assicuri che la macchina sia sempre carica di lavoro, un’altra che verifichi non vi siano dei malfunzionamenti e una terza che trasferisce i programmi e supporta le altre due figure – spiega Pedruzzi -. Se devi fare una produzione in serie, l’unica chance è affidarsi alle macchine perché nel disegno di un campo da padel rientrano circa quaranta tipologie diverse di pezzi e tutti devono essere perfetti per non avere problemi nella fase di montaggio». L’ingegno umano è invece necessario nella fase di progettazione perché la macchina non sbaglia ma esegue ciò che l’uomo le ha ordinato: «La problematica maggiore è il rispetto completo della NTC 2018, una normativa molto stringente perché correlata ai criteri utilizzati per costruire un edificio. Per dire, la struttura deve resistere a una spinta orizzontale di 300 kg per ogni metro lineare: per andare oltre questi limiti, bisognerebbe lanciarsi contro il campo con un camion! Per questo i campi da padel sono estremamente sicuri – dice ancora Pedruzzi -. Tuttavia, non rispettarla può avere conseguenza gravi, anche in caso di sinistro accidentale: è ciò che devono capire i gestori di un impianto padel». Accorgimenti che hanno un prezzo e necessitano di verifiche continue, a dimostrazione della qualità della filiera che, va sottolineato, è interamente made in Italy. Perché se si compra un campo all’estero e si verifica un problema, l’assistenza non è così pronta e garantita.
Un altro aspetto fondamentale è il processo di saldatura. Per quanto possa avere un profondo rispetto per la figura del saldatore, è chiaro che vedere un braccio meccanico che esegue il lavoro, infonde maggior fiducia sulla qualità del prodotto finale: «Quel braccio non si stanca, non si lamenta e lavora anche nei week-end – dice con un sorriso Pedruzzi -. Il robot viene guidato una prima volta, poi memorizza i movimenti: semplicemente, non può sbagliare». A certificare la bontà del lavoro, il 10% dei pezzi della produzione sono testati con dei liquidi penetranti che servono a controllare i difetti nelle saldature, benché l’affidabilità potrebbe concedere di sorvolare sulla questione: «Però fa parte dei servizi che offriamo per rassicurare il cliente» sostiene Pedruzzi.
Il passaggio successivo è uno dei più significativi e dalla provincia di Bergamo ci siamo spostati in quella limitrofa di Brescia, a San Gervasio, dove ha sede la Nord Zinc, zincheria che è diventata un vero punto di riferimento nel settore a livello nazionale. La zincatura, rigorosamente a caldo per i campi da padel, è un trattamento metallurgico che protegge dalla ruggine, da realizzarsi secondo le nuove normative internazionali e gli ormai determinanti requisiti di sostenibilità ambientale, soprattutto quando si tratta di processi dove il consumo energetico è inevitabilmente significativo. Il nostro Cicerone è Alessio Pesenti, direttore marketing e tecnico esperto di Nord Zinc: «Usiamo un ciclo brevettato per un processo che è una fusione di un metallo su un altro metallo. L’immersione nello zinco è totale in modo che il pezzo sia protetto interamente, altrimenti il rischio è di avere un ottimo risultato estetico ma di consegnare un tubolare dove all’interno si crea condensa dalla quale parte la ruggine. E quando si consuma lo spessore, il rischio è che la struttura possa crollare. La zincatura a caldo, realizzata ad arte, evita tutto questo».
Come avviene questo processo? Lo abbiamo seguito live: il pezzo di acciaio grezzo viene infilato in una vasca alla temperatura di 50 gradi per sgrassarlo e lavarlo, poi nella vasca di decapaggio, con acqua e acido cloridrico che porta l’acciaio a nudo, pronto per ricevere la zincatura a caldo. Quindi si passa allo sciacquo e a una successiva immersione con cloruro di ammonio, un sale che permette all’acciaio di arrivare alla vasca di zincatura privo di qualsiasi ossidazione («Terminato il decapaggio, l’acciaio nudo è molto reattivo: se restasse all’aria anche solo per qualche ora, arrugginirebbe in maniera incredibile» dice Pesenti). A questo punto, il pezzo viene calato nel forno di asciugatura per abbassare lo shock termico e si può procedere con il bagno di zinco che avviene in una vasca lunga tredici metri, larga cinque e profonda tre e mezzo, a una temperatura di 450 gradi. «La qualità della zincatura dipende al 50% dal tipo di acciaio – continua Pesenti -. Sulla sua superficie si trovano carbonio, silicio e fosforo che si legano con lo zinco: per esempio, se c’è troppo silicio, si carica tantissimo zinco e si formano delle croste, se è troppo poco, non si crea la protezione adatta. Non sono dettagli».

Il campo Italgreen installato alla fiera Padel Trend di Milano
Of course, il processo di zincatura deve seguire una precisa normativa e ricevere le adeguate certificazioni: «Il processo circolare consente di non sprecare risorse – spiega Psenti -. Se un campo venisse smantellato, potremmo recuperare lo stesso quantitativo di ferro utilizzato, senza alcuna perdita di materia prima». E non solo: «Oltre alla certificazione europea, unico caso in Europa, disponiamo della dichiarazione ambientale di prodotto (EPD, Environmental Product Declaration) in quanto possiamo dichiarare la quantità di CO2 impiegata per produrre e proteggere l’intera struttura in acciaio del campo. La nostra azienda è anche registrata all’EMAS, un regolamento europeo per la gestione degli impianti dove un’azienda si impegna ad abbassare l’inquinamento industriale, studiando nuove tecnologie di produzione. Insomma, Nord Zinc ha lo sviluppo sostenibile nel suo DNA visto che la zincatura a caldo è un processo molto pesante dal punto di vista energetico: solo per la corrente, consumiamo circa un milione di kwatt all’anno».
C’è un altro concetto piuttosto chiaro e che lega la zincatura alla verniciatura: la prima va eseguita col 99% di zinco e l’1% di altri metalli leganti. «Ecco, quell’1% può essere diverso per ogni zincatore e questa miscela crea una lega che dovrà essere verniciata – spiega Pesenti –. Ora, se non si conosce perfettamente la lega, il trattamento chimico potrebbe non funzionare e la vernice appoggiarsi ma non attaccarsi». Va da sé che se lo zincatore non comunica le esatte specifiche, al verniciatore non resta che affidarsi alla buona sorte. Inoltre, non dovrebbe nemmeno passare troppo tempo tra zincatura e verniciatura perché lo zinco è un materiale instabile: basta dell’aria umida e l’ossidazione impedirebbe di trattarlo chimicamente per verniciarlo. Per questo Nord Zinc, unica in Europa, ha creato il sistema Triplex che combina questi due passaggi: «Tra i due processi passano circa 24 ore e le vernici a polvere sono studiate specificamente per l’applicazione sullo zinco. In ambiente rurale garantiamo oltre cent’anni con un massimo dell’1% di ruggine; vicino al mare, data l’aggressione della salsedine, serve invece un trattamento specifico. Un buon esempio è il lavoro svolto per il Forte Village in Sardegna, dove la vernice si è aggrappata perfettamente e non ha mai subìto alcun danno» dice con una certa fierezza Pesenti.

La sede di Italgreen a Villa D’Adda, provincia di Bergamo
Il primo passaggio è un pre-trattamento di pulizia e un’applicazione nanotecnologica per preparare lo zinco alla verniciatura. Dopo sarà necessario un risciacquo e l’asciugatura in forno. Metallo e vernice devono cuocere allo stesso modo per 30-40 minuti. A quel punto il gioco è fatto: la vernice a polvere è un film che, rispetto a quella liquida, crea uno spessore decisamente più ridotto e quindi è meno soggetta a graffi e scalfiture. Un altro aspetto da considerare, è il colore da applicare: «Possiamo soddisfare qualsiasi esigenza però l’ideale è rimanere nella gamma dei venti colori del sistema Triplex. Altrimenti i costi aumentano perché bisogna fermare per circa 40 minuti un impianto che costa 2.300 euro l’ora – spiega Pesenti -. Ma non solo perché sullo zincato, servono vernici adatte: quelle a polvere nascono per l’alluminio, quindi un colore specifico deve essere riformulato. Per esempio, il flash green di Italgreen ha richiesto una riformulazione per il colore e per la componente chimica».
Processi raffinati, normative stringenti da rispettare, automazione robotica e professionalità umana: Italgreen, celebre per la sua erba sintetica con la quale ha ricoperto centinaia di campi sportivi, ha creato una filiera per la costruzione dei campi da padel innovativa e molto performante. Assistere a un intero processo produttivo ci ha permesso non solo di verificarne la qualità, ma anche di comprendere meglio la sua complessità e a generare un certo rispetto la prossima volta che entreremo in un 20×10. Perché i campi sembrano tutti uguali, ma non è assolutamente vero.
- 1.Le basi per un buon rovescio da fondo campo
- 2.Il nuovo Padel Pavilion di CityLife? Inizio lavori a maggio, apertura nel 2025
- 3.Altra sorpresa al P2 di Bruxelles: Yanguas e Garrido battono Stupa/Di Nenno e volano in semifinale!
- 4.Colpo di scena al P2 di Bruxelles: Sanz e Nieto eliminano Lebron/Paquito!
- 5.Campi da padel chiusi per rumore. La soluzione Padel Corporation. O le Olimpiadi…